نحوه پیشگیری از خطرات تولید میلگرد با بهرهگیری از فناوری نوین
فناوری های نوین در صنعت فولاد؛ الزامات و روش ها و نقش آن در کاهش قیمت میلگرد
به نقل از آسرون موافقتنامهی اقلیمی پاریس که این روزها بسیار مورد توجه قرار گرفته، یکی از محرکهای بنگاههای اقتصادی بزرگ دنیا به سمت توسعه پایدار و صنعت سبز است؛ بر اساس مفاد این موافقتنامه، کشورهایی که به آن پیوستهاند، موظفاند که از مقدار تولید گازهای گلخانهای که موجب گرمایش جهانی میشود، به مقدار قابل توجهی بکاهند. معدن و صنایع وابسته به آن، از جمله صنایعی هستند که همواره با چالشهای زیستمحیطی روبه رو بودهاند و طی سالهای اخیر، بنگاههای اقتصادی فعال در این حوزه برای تداوم نقشآفرینی در این عرصه، به سوی صنعت سبز و کمکربن گرایش پیدا کردهاند. تصویب این معاهده موجب قیمت آهن به صورت موقت شد.
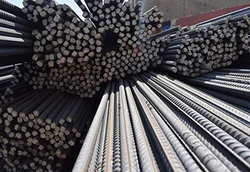
مجله حقوقی بینالمللی/ شماره ۶۰ نوشتهاست:
«موافقتنامه پاریس در خصوص تغییر اقلیم به صورت معاهده مکتوب در ۲۹ ماده در سال ۲۰۱۵ تقریباً با اجماع جهانی پذیرفته شد. هدف موافقتنامه، تقویت واکنش جهانی نسبت به تهدیدات ناشی از تغییر اقلیم و گرمایش زمین ناشی از افزایش گازهای گلخانهای است.
بنابراین به موجب این موافقتنامه و برای محدودکردن افزایش دمای کره زمین، مقرر شد که کشورهای جهان، برنامههایی برای کاهش انتشار گازهای گلخانهای ارائه دهند. موافقتنامه پاریس نشانگر رویکردی جدید در حکمرانی اقلیمی جهانی است که تمایز میان کشورها و واقعیات مربوط به درجه توسعهیافتگی آنها را میپذیرد اما مرزبندیهای پروتکل کیوتو را درنوردیده و تعهدات مشترکی را در خصوص کاهش انتشار گازهای گلخانهای، انطباق با تغییرات اقلیمی و شفافیت برای همه کشورها ایجاد میکند و جهت تعیین میزان و شکل تعهد که در ارتباط با واکنش اقلیمی از طریق برنامههای مشارکتی به عهده خواهند گرفت، استقلال بیشتری به آنها میدهد.»
این مجله همچنین اشاره کرده است که این موافقتنامه برخلاف ضمانت اجراهای حقوقی، برای تضمین اجرای آن از سازوکار «شرمندهسازی» استفاده میکند و با وضع قواعد شفافیت و بازنگری اجباری، خطر حیثیتی ایجاد میکند؛ به این صورت که شفافسازی و در معرض داوری دیگران قرار گرفتن باعث سرزنش عمومی و عدم اقبال جهانی به همکاری و تعامل اقتصادی با کشورهایی شود که آن را رعایت نمیکنند.
تحقق «هیدروژن سبز» یک باید است!
اردشیر سعدمحمدی، مدیرعامل گروه سرمایهگذاری توسعه معادن و فلزات، با اشاره به پیوستن ایران به معاهده اقلیمی پاریس و لزوم پایبندی به آن جهت ادامه تعاملات اقتصادی در دنیا، بیان کرد: در صورتی که صنایع ما نتوانند تا زمان مقرر، از تولید گازهای گلخانهای بکاهند، محصولاتمان در دنیا خریدار نخواهد داشت؛ بنابراین سرمایهگذاری برای تحقق صنعت سبز، یک ضرورت است.
سعدمحمدی ادامه داد: حدود ۷ تا ۹ درصد گاز گلخانهای در دنیا به دست صنعت فولاد تولید میشود. بر اساس تعهداتمان در معاهده پاریس، تا سال ۲۰۳۰ باید تولید گاز کربن دیاکسید توسط صنایع ما، ۵۰ درصد کاهش یابد.
مدیرعامل «ومعادن» بیان کرد: به ازای تولید هر تن فولاد خام، در روش کوره بلند BF (کورههای اکسیژنی مبتنی بر گاز و زغال سنگ) ۱.۵ تا ۲.۳ تن، کورههای اکسیژنی SR (حذف واحد کلوخهسازی و ککسازی در فرایند فولادسازی) ۰.۹ تا ۱.۳ تن و در روش احیاء مستقیم ۰.۶ تا ۱.۵ تن گاز آلایندهی کربن دیاکسید تولید میشود.
سعدمحمدی تاکید کرد: موضوع استفاده از هیدروژن به عنوان منبع تولید انرژی مورد نیاز صنایع، در دنیا بسیار جدی است و اکیداً مورد توجه صنایع قرار گرفته است؛ ما نیز موظفیم با همه محدودیتهای موجود و هزینه بسیار بالایی که دارد، تمام تلاشمان را در راه تحقق آن به کار بگیریم.
وی افزود: در فرآیند احیای مستقیم میدرکس، استفاده از انرژی پاک هیدروژنی کاملاً عملیاتی و تسهیل شده است و با همان تجهیزات موجود و بدون نیز به اصلاحات، می توان با وارد کردن هیدروژن، استفاده از گاز طبیعی را تا ۳۰ درصد کاهش داد.
سعدمحمدی ادامه داد: سیر تکاملی میدرکس در جهت جایگزینکردن صد درصدی هیدروژن با گاز طبیعیست و دارد اصلاحاتی در تجهیزات آن صورت میگیرد که در این صورت نسبت به روش کوره بلند BF، کاهش ۸۰ درصدی در تولید آلاینده CO2 را به همراه خواهد داشت.
مدیرعامل «ومعادن» ضمن اشاره به فرآیند تکنولوژی Flash که تا پیش از این برای عناصری چون مس، سرب و روی استفاده میشد، بیان کرد: این تکنولوژی تحولآفرین که کاهش چشمگیر مصرف انرژی و تولید CO2 را به دنبال دارد، اکنون وارد صحنه بازی سنگ آهن نیز شده و به سرعت در حال توسعه است.
وی افزود: این فناوری نسبت به روش کوره بلند فعلی، پتانسیل کاهش مصرف انرژی به میزان ۳۲ تا ۵۷ درصد و کاهش انتشار کربن دیاکسید به میزان ۶۱ تا ۹۶ درصد را داراست.
مدیرعامل «ومعادن» ادامه داد: یکی دیگر از فناوریهای نوین، تولید آهن مذاب به روش الکترولیز است که در این روش، ابتدا سنگ آهن در یک محلول الکترولیت حل شده و سپس با عبور جریان برق، امکان جداسازی آن فراهم میشود و محصولات این واکنش آهن فلزی و اکسیژن خواهد بود.
سعدمحمدی در ادامه به انواع روشهای تولید گاز هیدروژن در صنعت و محدودیتهای آن اشاره کرد و گفت: تا پیش از سال ۲۰۲۰، گاز هیدروژن عمدتاً از احتراق گاز طبیعی حاصل میشد که به دلیل تولید همزمان گاز آلاینده CO2 به آن هیدروژن خاکستری میگویند.
وی افزود: در روش دیگر، با فناوری CCUS (carbon capture, utilization and storage – جذب کربن، استفاده و ذخیره آن) کربن تولیدشده از احتراق گاز طبیعی و سوختهای فسیلی از دودکشها جذب شده و در زیرِ زمین ذخیره میشود که هیدروژن ماحصل آن، هیدروژن آبی نامیده میشود.
سعدمحمدی با بیان اینکه روش مطلوب ما فرآیندی است که تولید CO2 در آن به صفر میل کند، به روش الکترولیز آب اشاره کرد و گفت: ۴ درصد از تولید جهانی هیدروژن از این مسیر به دست میآید؛ از آن جایی که هیدروژن از مولکولهای آب حاصل میشود و نه هیدروکربنها، به آن هیدروژن سبز گفته میشود و هیچ گاز آلایندهای وارد محیط زیست نمیکند.
مدیرعامل شرکت سرمایهگذاری توسعه معادن و فلزات تاکید کرد: تأمین هیدروژن از روش الکترولیز برای تحقق اهداف صنعتی، به برق بسیار زیادی نیاز دارد که باعث شده روش بسیار پرهزینهای باشد و نیازمند سرمایهگذاری هنگفتی است.
وی افزود: علاوه بر آن، برای تحقق «هیدروژن سبز»، انرژی برقی که استفاده میشود باید از روشهای تجدیدپذیر و بدون استفاده از سوختهای فسیلی تولید شده باشد که این پیشنیازها دستیابی به آن را برای ما بسیار پرهزینه میکند اما پیوستن به این مسیر یک باید است؛ در غیر این صورت در صادرات محصولاتمان دچار مشکلات جدی خواهیم شد.
سعدمحمدی در پایان بیان کرد: بر اساس پیشبینیهای انجام شده، تولید فولاد خام از ۱.۸۶۷ میلیارد تن در سال ۲۰۲۰ به ۲.۱۸۷ میلیارد تن در سال ۲۰۵۰ خواهد رسید. فولادسازی به روشهای فعلی بین سالهای ۲۰۴۵ تا ۲۰۵۰ متوقف شده و تنها از روشهای نوظهور و فناوریهای تولید فولاد سبز استفاده خواهد شد.
نگاهی به تولید میلگرد ساده
در تولید میلگرد ساده یکی از مهمترین فاکتورهای تعیین کننده کیفیت و قیمت میلگرد ساده ، فرآیند تولید این محصول است. آشنایی با چگونگی تولید میلگرد و روش های گوناگون آن می تواند در هنگام انتخاب و خرید میلگرد به ما کمک کند.
انواع میلگرد سری A
میلگردها را می توان با توجه به مشخصات ظاهری، خواص مکانیکی و خواص شیمیایی آنها دسته بندی کرد. بر اساس ویژگی های ظاهری، میلگردها به انواع میلگرد ساده و میلگرد آجدار تقسیم می شوند. تقسیم بندی میلگرد ها بر اساس خواص شیمیایی و مکانیکی به این صورت است:
- میلگرد A1 (میلگرد ساده ۲۴۰)
- میلگرد A2 (میلگرد آج ۳۴۰)
- میلگرد A3 (میلگرد آج ۴۰۰)
- میلگرد A4 (میلگرد آج ۵۰۰)
خط تولید میلگرد ساده
در تولید فرآورده های فولادی چون میلگرد ساده، همواره از بلوک های فولادی استفاده می شود. در حقیقت پیش از تولید میلگرد، فولاد را به شکل شمش یا بلوک در می آورند تا جابجایی و فرم دهی آن به سهولت انجام شود. در خط تولید میلگرد ساده فرم دهی فولاد و تولید محصولات فولادی با استفاده از روش هایی چون نورد، کشیدن، پرس و آهنگری صورت می گیرد. در همه این روش ها از شمش های فولادی استفاده می شود. شمش های فولادی خود با استفاده از قالب یا به شیوه ریخته گری مداوم تولید می شوند.
کیفیت مواد اولیه در تولید میلگرد ساده
کیفیت مواد اولیه اهمیت زیادی در تولید مقاطع فولادی دارد. معمولاً مشخصات مواد اولیه به نوع مقطع فولادی بستگی دارد. برای نمونه میلگرد ساده با استفاده از شمش های 3SP تولید می شود. در صورتی که در ساخت انواع تیرآهن، نبشی و ناودانی از شمش های فولادی 5SP استفاده می شود. ابعاد شمش های مورد استفاده در تولید میلگرد ساده معمولاً ۱۵۰۱۵۰۶۰۰۰ یا ۱۲۵۱۲۵۶۰۰۰ است. انتخاب ابعاد شمس با توجه به خط نورد و ظرفیت کوره انجام می شود. به طور معمول این شمش ها را با طول ۱۲ متر برش داده و برای فرآوری آماده می کنند. پس از آماده شدن شمش ها، عملیات تولید میلگرد ساده آغاز می شود.
روش های مورد استفاده در تولید میلگرد ساده
میلگرد ساده را می توان با روش های گوناگونی تولید کرد. فرآیند نورد از متداول ترین شیوه هایی است که برای این منظور به کار می رود. در طی این فرآیند فولاد از میان غلطک عبور کرده و شکل می گیرد. فرآیند نورد می تواند به صورت سرد یا گرم اجرا شود. نورد سرد یعنی فرم دهی فولاد در دمای محیط و نورد گرم یعنی فرم دهی فولاد در دمای بالاتر از دمای محیط. البته در نورد گرم دما باید از دمای ذوب فولاد کمتر باشد. مزیت های نورد موجب شده که به عنوان یک شیوه رایج در تولید محصولات فولادی مطرح باشد. بازدهی زیاد و دقت بالا در کنترل فرآیند تولید از جمله مزیت هایی است که نورد سرد و گرم به همراه دارند.
نورد گرم
نورد گرم به عنوان یک روش رایج در تولید انواع میلگرد شناخته می شود. در این شیوه شمش های فولادی را تا دمای ۱۱۰۰ درجه حرارت داده و ذوب می کنند. برای این منظور با استفاده از جک هیدرولیکی شمش ها را در داخل کوره قرار می دهند. حرارت کوره شمش ها را برای عملیات نورد گرم آماده می کند. عملیات نورد گرم طی مراحل مشخصی انجام می شود. در ابتدا شمش ها تحت اعمال فشار و کشش قرار می گیرند. این کار موجب می شود قطر آن ها کم شده و در عوض طولشان افزایش پیدا کند.
عملیات آج زنی در نورد گرم
در مرحله بعد و در صورت تولید میلگرد آجدار، عملیات آج زنی بر روی میلگرد انجام می شود. برای این کار ابتدا میلگرد را خنک کرده و در دمای معمول محیط آن را آجدار می کنند. در ادامه با استفاده از قیچی برش، میلگردها را برش می دهند. در این مرحله طول میلگرد ها ۲۴ یا ۳۶ متر است. در نهایت میلگردها را به اندازه استاندارد یعنی ۱۲ متری در می آورند و دسته بندی می کنند.