انواع روش ها و فرآیندهای تولید لوله فولادی
لوله بدون درز یا مانیسمان با فرایند جوش تولید نمیشوند. فرآیند تولید لولههای بدون درز در پایان قرن نوزدهم توسعه یافت. به رغم بسیاری از آزمایشات قبلی، آزمایشها و فن آوری ها، اختراع فرآیند سوراخ کردن یا سنبه زنی متقاطع لوله بدو ن درز توسط برادران مانسمان تا پایان سالهای 1880 به طور گستردهای به عنوان نشانهای از شروع تولید مقیاس بالا تولید لولههای بدون درزشناخته شده است. در فرآیند سوراخ کردن شمش، محور نورد موازی با محور شمش، یک بخش از فرایند تولید است. با چرخش در همان جهت، این نورد یک مسیر اسپیرال برای عبور شمش از طریق شکاف رول ایجاد کرده است. علاوه بر این، سرعت خروج در حدود 10 برابر سرعت دورانی قلتک کاهش یافته است.
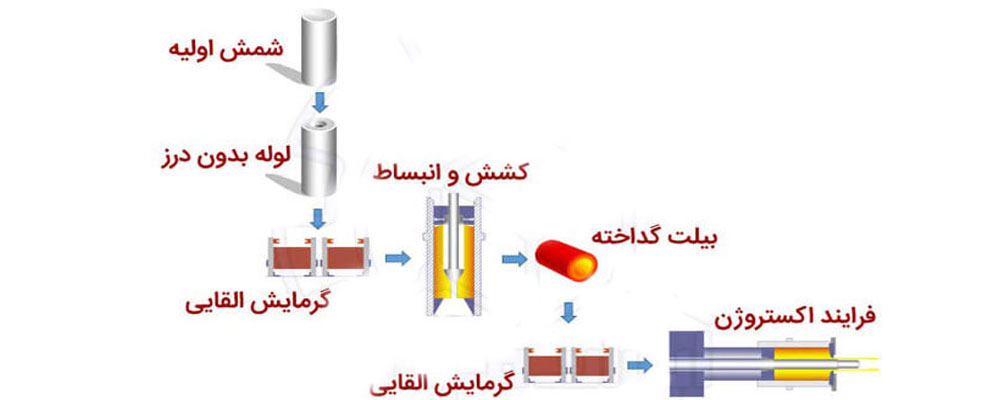
با معرفی یک هسته سنبه مانند که در فاصله بین قلتک ها مرتب شده است، مواد اولیه جامد دوار را میتوان برای ایجاد یک پوسته توخالی در حین نورد گرم توسط عمل قلتک کاری و گردش همزمان سوراخ کرد. با این حال هنوز نمیتوان لولههای با ضخامت دیوارههای معمولی را در طول مدنظر توسط فرایند سوراخ کردن و سنبه زنی به تنهایی تولید کرد. در حال حاضر لوله بدون درز (مانیسمان) از شمش گرد ساخته شده است، که از طریق سنبه زدن مرکز سوراخ شده است تا پوسته توخالی ایجاد شود و سپس نورد یا اکسترود شده و به اندازه مد نظر کشیده میشود. فرایند تولید لوله بدون درز متشکل از مراحل اصلی زیر است.
- ساخت پوسته لوله توخالی در عملیات سنبه زنی یا اکستروژن
- پانل لوله توخالی را با کاهش قطر و ضخامت دیواره، کشیده میشود
- ساخت یک لوله نهایی در روند نورد گرم یا سرد
همانطور که حق انحصاری این فن آوری منقضی شده، تحولات مختلف در فرآیند تولید شکل گرفت و مراحل تشکیل آنها به فرآیندهای جدید ادغام شدند. امروزه فرایندهای تولید لوله بدون درز (مانیسمان) به سطوح مختلفی توسعه یافته است که این فرایندها به حالت مدرن فرآیندهای با کارایی بالا تبدیل شده است. بسته به اندازه لوله، ترکیب محصول و همچنین در دسترس بودن مواد اولیه، امکانات جدیدی برای تولید لوله بدون درز (مانیسمان) ساخته شده است. روند نورد مداوم و فرآیند سنبه زنی در محدوده اندازه گیری از حدود 21 میلی متر تا 178 میلی متر قطر خارجی صورت میگیرد. فرآیند چند مرحلهای سنبه زنی با سنبه استوانهای معلق در سایزهایی از 140 میلیمتر تا 406 میلیمتر در قطر خارجی موجب توخالی سازی میشوند.
فرآیند سنبه زنی و قلتک زنی جهت فرم گیری لوله شکل 1-فرآیند سنبه زنی و قلتک زنی جهت فرم گیری لوله در این فرایند، شمشها در یک کوره چرخشی به دمای 1250 تا 1300 درجه سانتیگراد گرم میشوند. قبل از کوره شمشها از با فشار آب تمیز میشود و به کارخانه سوراخکاری با سنبه منتقل میشود که در آن شمش سوراخ شده وپوسته توخالی ضخیم دیوار تولید میکنند. در این فرایند محصول خام اولیه را به طول 1.5 تا 2 برابر طول میکشد و سطح مقطع بین 33 تا 50 درصد کاهش مییابد. کارخانه سوراخکاری دارای دو نورد قلتک زنی میباشد که مخصوص کشیدن لوله طراحی شده است که در همان جهت چرخش هدایت میشوند.
محورها در حدود 3 تا 6 درجه نسبت به خط نورد افقی قرار دارند. فاصله بین قلتک ها به طور کلی توسط یک قلتک پشتیبانی بدون کنترل کننده در بالا و یک کفی پشتیبانی در پایین محکم محصور و بسته شده است. یک نقطه سنبه زنی که به عنوان یک ابزار داخلی عمل میکند در مرکز شکاف رول واقع شده و توسط یک بلوک رانش خارجی از طریق یک هسته سنبه مانند در موقعیت مرکز قرار گرفته است. پوسته توخالی با دیواره ضخیم پس از عملیات سوراخ کردن دوباره در ایستگاه پلانگر قلتک زنی میشود تا تولید لوله به پایان برسد. نسبت طول دهی در طی فرایند قلتک زنی بین 5 تا 10 است و با کاهش مقطع 80 تا 90 درصدی همراه است. نورد تولید کننده یک قطر خارجی دقیق را تولید میکند و همچنین باعث افزایش مرکزیت و دوار شدن لوله میشود.
خط قلتک زنی دارای دو قلتک است (گاهی اوقات به خاطر عمل پرسی به عنوان قالب شناخته میشود) با شکل مخروطی در اطراف قلتک. قلتک ها به سمت حرکت متقاطع مواد خام تنظیم میشوند. دمای کاری بین 200 تا 220 درجه برای اطراف قلتک ها قرار دارد و شامل ورودی مخروطی شکل، یک سیلندر و یک هموار کننده است که در یک محفظه بزرگتر برای آزاد کردن قطعه کار قرار دارد. فرایند قلتک زنی فرم دهنده یک فرآیند فورجینگ نوردی مرحلهای است که با چرخش قطعه به عقب و جلو عمل میکند. پس از اتمام فرایند پلانگر یا قلتک فرم دهنده، لوله نهایی شده از سنبه خارج میشود. بخشی از پوسته توخالی شناخته شده به عنوان بریده میشود. پس از حرارت دادن آن در یک کوره، لوله به اندازه مناسب در خط نورد کاهش مییابد.
این معمولاً شامل سه مرحله با دو یا سه قلتک دقت بالا میباشد. نورد یک مسیر عبور بسته را (در تنظیمات چندین ایستگاه) تشکیل میدهند که هر کدام از آنها یک زاویه را با خط نورد قبلی تنظیم میکنند. در نورد کاهشی یا کششی، قطر خارجی لوله به طور قابل ملاحظهای کاهش مییابد و ضخامت دیواره کمی افزایش یا کاهش مییابد. بسته به نوع محصول، کارخانجات دارای 5 تا 28 مرحله نورد هستند. پس از آخرین عملیات فرم دهی، لولههای به پایان رسید به دمای محیط در یک بستر خنک کننده، خنک میشوند و پس از بررسی دقیق به بخش تکمیل منتقل میشود که در آن فرآیندهای مانند ماشینکاری پایان لوله، هموار کردن و آزمایش هیدرولیکی انجام میشود.
در مورد لولههای با قطر بزرگ که مواد ورودی معمولاً از یک شمش چند ضلعی است استفاده میشود. این شمش پس از حرارت دادن در یک کوره دوار در ابتدا به یک قابل مدور با سنبه عمودی وارد میشود. شمش جامد توسط یک پانچ استوانهای تحت پرس قرار میگیرد و تقریباً نیمی از قطر سوراخ ایجاد شده و یک پوسته توخالی با یک پایه بسته تولید میشود. عملیات بعدی شامل کاهش ضخامت دیواره همراه با درجهٔ کمی از کشیده شدن طول لوله در نورد است. در طول این فرایند، پایان لوله سوراخ شده است. پس از آن، پوسته توخالی در خط قلتک فرم دهنده شکل لوله را به خود میگیرد و سپس عملیات اندازه گیری و برش صورت میگیرد. فرآیند نورد پلاگین یا فرایند کشیدن
فرآیند نورد پلاگین یا فرآیند کشیدن
در این خط سوراخکاری در یک مرحله انجام میشود تا یک پوسته توخالی دیوار نازک ایجاد شود که طول آن تا 3 تا 4.5 برابر طول اصلی آن است و سطح تغییرات 65 تا 75 درصد میباشد. خط سنبه زنی دارای دو قلتک پیش ران است که دارای یک مسیر گذر دوطرفه است. محورهای قلتک موازی با خط نوردهستند و از 6 درجه تا 12 درجه به سمت افقی حرکت میکنند. شکاف بین رولهای کاری با استفاده از یک بستر راهنمای بالا و پایین تنظیم میشود. به علت نوسانات بازار جهت مشاهده قیمت آنلاین آهن آهن رسان و دیدن همه محصولات میتوانید وارد سایت آهن رسان شوید .
این کفشکهای هدایت کننده به فرایند کشش کمک میکنند و به عنوان قلتکهای ثابت عمل میکنند، به طوری که قادر به تولید یک پوسته توخالی نازک است. محصولی که از قلتک بیضوی عبور میکند خط نورد را دنبال میکند، و به سنبه این اجازه را می ده تا به عنوان یک ابزار داخلی عمل کند به طوری که میتواند به عنوان یک ابزار داخلی عمل کند تا لوله را به طور موثری تشکیل دهد. سنبههای جدید تنها یک بخش سوراخکاری مخروطی با قلتک های کاری با طراحی دوجهت دارند چرا که آنها هر یک در حدود 30 درجه با محصول در حال تولید زاویه دارند. و 10 تا 12 درجه نسبت به افق مورب هستند. فاصله موجود در نورد با دو دیسک جانبی کهان دو نیز متحرک هستند محصور شده است
فرآیند نورد پیوسته پس از برداشتن سنبه، لولههای نورد قبل از پردازش در خط اندازه گیری یا نورد کاهنده یا کشش دوباره گرم میشوند. کارخانه کشش که در ساخت و ساز مشابه کارخانه نورد مداوم است از دوازده قلتک پایه بلند تشکیل شده است. کاهش تنش تکنیکی منحصر به فرد است چرا که بدون استفاده از یک تکیه گاه و نگهدارنده سنبه ضخامت دیواره کاهش مییابد در حالی که قطر لوله نیز همزمان کاهش مییابد. نیروی کششی که لوله در بین آن قرار میگیرد نه تنها در کاهش ضخامت دیواره لوله مؤثر است بلکه کاهش قطر انجام شده در هر مرحله را میتوان سه برابر کرد. در شکل ذیل شما 4 مرحله از فرایند نورد و قتک زنی جهت فرم گیری پوسته ایجاد شده پس از سنبه زنی را مشاهده میکنید که مرحله به مرحله بعد از تکمیل عملیات توخالی سازی در طی مرحله نورد دقیق، لوله شکل و فرم نهایی خود را میگیرد و به صورت کاملاً دایره شکل تبدیل میشود.
فرآیند کاهش و اندازه گیری برای لولههایی با قطر کوچک استفاده میشود. از آنجا که سوراخ کردن، نورد و برش لولههایی با قطر کوچک اقتصادی نیست، تولید لولهها با نورد گرم با قطر کمتر از حدود 75 میلی متر قطر نیاز به یک فرآیند کاهش و اندازه گیری دارد که در آن یک ماشین ویژه کار میکند. این دستگاه مشابه خط نورد مداوم است. این ترکیب از 8 تا 16 مرحله شامل 2 قلتک با شیارهایی بلند به قطر 305 میلی متر تشکیل شده است. برای قطرهایی از حدود 140 میلی متر و بالاتر، اندازه گیری برای اطمینان از اندازه و گرد بودن یکنواخت در طول لوله صورت میگیرد. بنابراین فرایند اندازه گیری صرفاً شامل عبور لوله از طریق دو یا سه پایه غلتک اندازه است که شیارهای آن کمی کوچکتر از لوله حلقه شده است. در بعضی موارد، گرم کردن مجدد لازم است.
در بعضی موارد، نورد و چرخش با فرآیندهای معمولی یعنی نورد مداوم جایگزین میشود، به عنوان مثال با 9 پایه پشتیبان جداگانه از قلتک های شیار بلند. پس از سوراخ کردن یک قطعه توسط خط سنبه زنی، یک سنبه روانکار که به میزان قابل توجه بزرگتر از پوسته سوراخ شده است، وارد میشود و هر دو ازخط نورد عبور میکنند. فرایند نورد مداوم شامل چندین پاس قلتک در یک سری از نوردهای چرخشی است تا یک خط نورد شکل بگیرد. این نوع نورد پوسته توخالی را که درخط سنبه زنی سوراخ شده را میکشد و توسط یک سنبه که به عنوان ابزار داخلی عمل میکند لوله فرم نهایی خود را میگیرد.
همچنین یکی از موارد پرکاربردی که بسیار رواج دارد مناطقی است که در معرض انفجار یا آسیب فیزیکی قرار دارند. ار، فرایند سوراخ و کشش، فرآیند اکستروژن لوله و فرآیندهای نورد متقاطع هستند. فرآیندهای نورد متقاطع شامل پروسه نورد مارپیچ و روند نورد با قالب است. علاوه بر این، لولههای بدون درز نیز با فرآیند فرم دهی سرد، طراحی سرد و فرایند فرم دهی با قالب طی نورد سرد تولید میشوند. در شکل بالا شما نمای کلی و خلاصه سنبه زنی و فرم دهی تا نورد جهت کشیدن پوسته توخالی ایجاد شده جهت رسیدن به قطر دلخواه را مشاهده میکنید.